Horizontal Drilling for Electrical Resistance Heating System
Aggressive removal of dense non-aqueous liquid (DNAPL) phase tetrachloroethylene (PCE) and trichloroethylene (TCE) under an active manufacturing
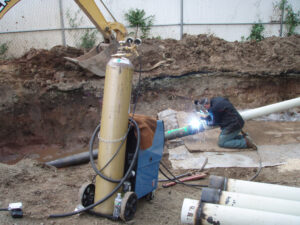
facility is the objective of an electrical resistance heating (ERH) system that was installed using horizontal drilling. Placement of electrical resistance heating electrodes within horizontal carbon steel pipe overcame concerns about traditional, vertically installed electrodes at the site:
- Drilling inside of the active facility would generate dust and cause vibration that would interfere with the precision machining and manufacturing work performed in the building,
- The labyrinthine distribution of multiple milling machines of many different shapes and sizes would interfere with vertical drilling work to install the ERH electrodes under the building,
- Interruption of the non-stop, 24-hour-a-day production schedule was unacceptable to the owners of the operation, who were not responsible for the plume beneath the building because it emanated from a neighboring former drycleaning facility, and
- A grid of vertical ERH electrodes would severely limit placement options for a horizontal soil vapor extraction (SVE) system that was required in order to prevent vapors generated by the ERH system from entering the indoor air of the manufacturing facility.
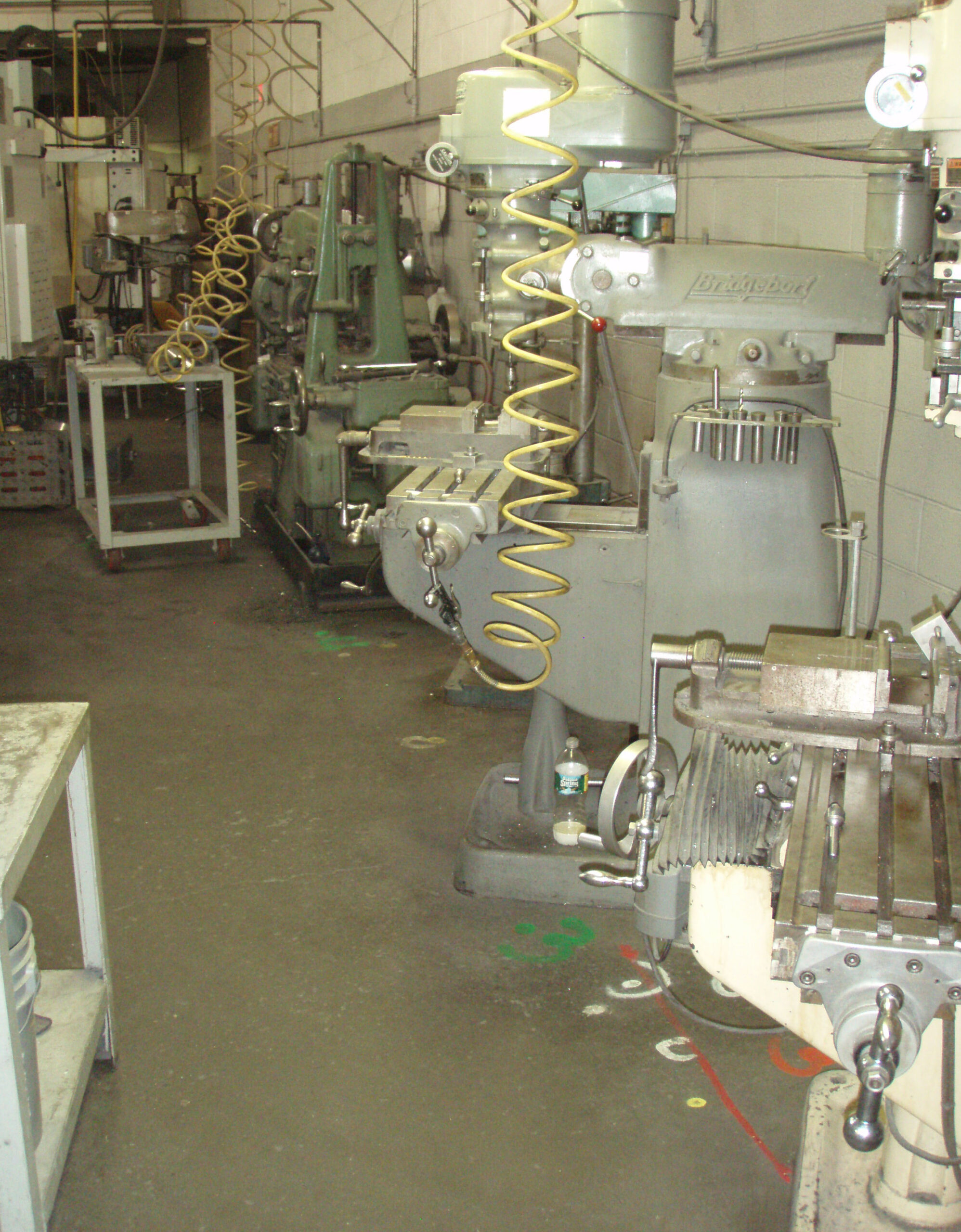
The Horizontal Solution to ERH Electrode Placement
Electrical resistance heating electrodes are distributed in the subsurface to create a network of triangular electrode groupings in cross section. The purpose of such a configuration is to optimize the distribution of heat across the target zone, from top to bottom. One set of electrodes is placed at a shallow horizon within the target zone, and another set is placed at a deep horizon. Shallow and deep electrodes are staggered, so that they don’t overlie each other.
Vertically the target zone reaches from 2 to 15 feet below ground surface (bgs), but horizontally it spans a 17,000 square foot area of the building. Electrodes are placed at only two different elevations, but multiple electrodes are placed along a given horizontal traverse. Installing electrodes within horizontal casings is therefore much more efficient than installing them in vertical casings. The flexibility of shifting electrodes within a horizontal casing that extends 200 feet across the building is an additional benefit of using horizontal drilling to install the electrodes. This flexibility will allow the electrical resistance heating to be optimized in the course of its operation, as some portions of the target zone remediate more quickly than others.
Hybrid ERH and horizontal SVE Wells
The shallow ERH pipes served double duty as horizontal soil vapor extraction (SVE) wells. Alternating sections of the pipe were slotted for SVE, or solid for ERH. This configuration avoided the logistical problem of threading SVE wells into the network of ERH electrodes.
Horizontal Electrode Pipe Installation
Heavy, rigid black steel casing with 6-inch diameter was used for installing the ERH system. Directional Technologies employed both blind and entry-exit installation methods for the horizontal ERH system. Each black steel casing was welded onto the casing string as it advanced into the wellbore. See the illustration at the top of this article. The shallow wells were only 3 feet below the building slab, so the drilling method was adapted to minimize communication through cracks in the foundation. A grout seal was emplaced around the pipe where it crossed below the building foundation in order to prevent short-circuiting of the horizontal SVE system. Installation of the deep wells 14 feet bgs in weathered sandstone and gravel formation was challenging because of the weight and limited flexibility of the black steel casing. In completing the ERH casing under the manufacturing facility, Directional Technologies Inc. brought to bear its 20 years of experience directionally drilling in every form of soil, sediment or igneous and metamorphic rock.
Round-the-clock site operations using sensitive milling equipment continued unabated by the directional drilling work in yet another example of Directional Technologies’ tradition of partnering with consultants and site owners/operators to ensure successful and unobtrusive remedial system operation.