There is no one size fits all when it comes to horizontal well systems. Site-specific conditions require customized horizontal wells to accomplish project remediation goals. This article explores the different types of horizontal well systems and the advantages these systems provide remediation projects.
There are two main types of horizontal well systems available to environmental professionals conducting site remediation:
- Engineered, custom slotted horizontal wells
- Prefabricated horizontal wells
Engineered, custom slotted horizontal wells are designed on a site by site basis, specifically for the subsurface conditions and remedial application desired. Prefabricated horizontal wells systems are available for purchase from the manufacturers. This article will discuss when and where each type of horizontal well system has its advantages and limitations.
Engineered, Custom Slotted Horizontal Well Systems
Engineered, custom slotted horizontal wells systems are highly versatile and can provide remedial solutions to widely varying site conditions including depths, lithology types, and contaminate types. These horizontal wells are typically constructed of high density polyethylene (HDPE) or polyvinyl chloride (PVC), but can also be constructed of fiberglass and stainless steel. Custom, software designed horizontal well screen materials are machine cut to the desired slotting and zoning specifications prior to being shipped to the site for installation.
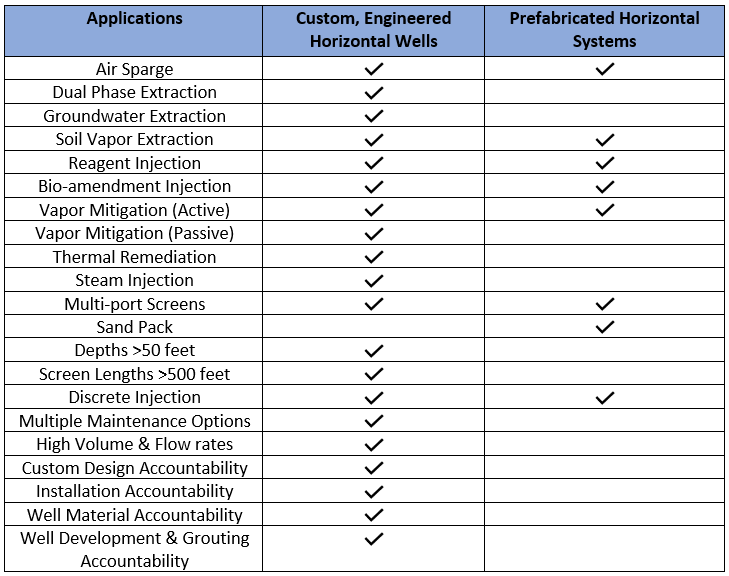
Engineered Custom Horizontal Well Advantages:
- Customizable horizontal well screen slotting provides even distribution of fluids along the screened section of the horizontal well.
- Can be used for multiple remediation techniques: air sparge, soil vapor extraction, chemical injection, bio-amendment injection, ozone/oxygen sparge, vapor mitigation (active and passive), dual phase extraction, groundwater pump and treat, thermal remediation, and steam/hot air injection.
- Able to design with multiple types of horizontal well materials at varying diameters, 2-inch to 10-inch diameters.
- Able to design multi-port horizontal wells (several horizontal wells in one borehole).
- Larger horizontal well diameters increase fluid flow and decrease friction loss.
- Larger diameter horizontal wells allow for an increased volume of injectables, which can expedite remediation.
- Large diameter wells allow for greater recovery rates in pump and treat applications.
- Horizontal well screens can be engineered to be 500 feet long and longer.
- Able to be installed blind (or single-ended) rather than a traditional entry-exit bore.
- Able to be installed at depths of greater than 50 feet.
- Multiple horizontal well maintenance options such as the installation of development pumps and jetting tools.
- During the design process, horizontal wells can be designed for multiple purposes, i.e. Air Sparge/Injection, SVE/Injection to provide different applications through one well screen.
Limitations of Custom Horizontal Wells
- Discrete injection within the horizontal well screen is possible but requires a packer device.
- Heterogeneous ground conditions may need additional site characterization data in order to maximize even flow distribution with customized horizontal well screen slotting.
- The requirement for filter sand pack can be overcome through a slot design appropriate for the formation, proper horizontal well development, and a proper operations and maintenance program.
Prefabricated Horizontal Systems
Several types of prefabricated horizontal systems (including segmented horizontal wells) are on the market. However, these products are limited in the remedial applications they can provide.
Prefabricated Horizontal Well System Advantages:
- Able to provide numerous well segments within one horizontal bore.
- Prefabricated and shipped to site.
- Allows for discrete fluid injection controlled at an injection system manifold.
- Can be used for chemical injection, air sparging, soil vapor extraction, and active vapor mitigation.
Limitations of Prefabricated/Segmented Horizontal Systems:
- Limited remedial options
- Limited conduit diameters, and limited volume. Typically, the conduits are 3/8-inch or ½-inch diameter and below, therefore injection is a low-flow treatment strategy, with discrete injection control over a longer duration.
- In most cases, requires entry-exit installation, and therefore requires an exit location for the horizontal bore.
- Limited airflow rates for AS/SVE applications.
- A grout seal must be successfully installed between well screen segments to ensure there is no fluid communication within the boring annulus. This can be difficult in a non-collapsing formation.
- Limited maintenance options due to small diameter tubing (screen sections cannot be scrubbed or surged).
Horizontal Well Performance Accountability
Regardless of the type of horizontal well system, the overall success of a horizontal remediation project will depend mostly on successful horizontal well design, horizontal well installation, development, and grouting. Horizontal well installations, when conducted with horizontal directional drilling, may be more complicated than typical vertical well installations.
Accountability for successful horizontal well performance should be shared between the entire project team. The design team, installation team, well material provider, and the well development team must all have a vested interested in a successful project.
If a horizontal well fails to perform as expected, how is each team held accountable?
The entire project team must understand how site challenges may affect the operation of the horizontal well system. A poor design, improper installation, and unsuitable well materials will lead to underperforming horizontal wells and will impede the overall objectives of the project.