How do you mitigate vapor intrusion with access limitations due to source area contamination residing beneath a large commercial building? It is not uncommon that environmental remediation sites are generated from contamination spills beneath a facility. When source-area contamination is beneath a building, a range of environmental problems arise. Contaminants can leach through the soil and impact groundwater, allowing mobility of the contamination to off-site locations. Vapor intrusion from beneath the facilities’ slab can create dangerous working conditions if vapors permeate inside the facility. The case study below is an exact representation of these conditions and an excellent demonstration of Directional Technologies’ utilization of blind installation technologies to overcome physical site constraints to meet the remedial objectives of the project.
Background and Setting:
At a facility located in the Midwest of the United States, a large chlorinated solvent contaminant release was discovered beneath the existing foundation of a factory building. Primary contaminants of concern included trichloroethylene (TCE) and cis-1,2-DCE, which accumulated because of a leak beneath the building. The consultant had been tasked with producing a remediation plan that would reduce source area soil contamination, but the obstructive location of the source area contaminants posed various difficulties. Soil conditions beneath the site were predominantly sandy with varying degrees of clay content.
Reducing Vapor Intrusion to Provide Safe Working Conditions
Mitigating vapor intrusion was the primary remedial goal, as vapor infiltration through the facilities’ sub-slab could have caused unsafe or impossible working conditions inside the building. Ongoing remedial efforts were insufficient in reducing contamination levels due to access complications with the location of the source area soil contamination being beneath a building. The consultant needed to find a way to gain access to the source but also needed to minimize interruptions to the daily activities of the active facility. Since the contamination was beneath the existing facility, traditional vertical methods were an insufficient means to achieve the remedial goals of the project. The source area soils required thorough and rapid remediation to prevent vapor intrusion into the active facility. In the event that air quality contamination reached levels that were above industrial standards, work would need to be halted in the facility, severely impacting business operations.
Designing the Remediation System
Directional Technologies was brought in as a collaboration partner to help design and implement a remediation system that would meet the remedial goals of the project. The primary objective of the horizontal system was to overcome the obstacle of the existing on-site facility and provide optimal access to the source area soil contamination beneath the building to mitigate vapor intrusion. One horizontal soil vapor extraction (SVE) well was installed in 2016 as part of a pilot study to assess remedial effects at the site. The well was installed via blind installation technology, meaning only an entry point was required, with the well terminating at the end of the screen below the ground surface. Blind installations are particularly useful at site locations where on-site obstructions prevent access to the contamination. Since an exit point for the well is not required, there is a major reduction in borehole linear footage and required materials, decreasing project costs while continuing to provide unparalleled access to the contamination.
The single horizontal SVE well acquired a radius of influence of 40 feet within the subsurface and immediately began reducing chlorinated solvent concentrations. Data showing successful results of the horizontal well were collected over the course of three pilot study steps, where TCE and cis-1,2-DCE concentrations were significantly reduced (Figure 1). However, the results of the pilot study confirmed there was significantly more contamination in the source area soils than the consultant expected. Vapor intrusion continued to be an environmental and business concern at the facility.
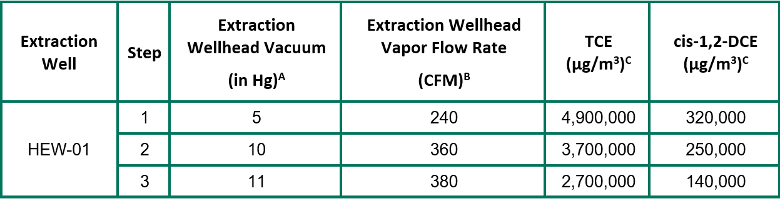
Due to the unexpected increase in contaminant concentrations, Directional Technologies was asked to return to the site in 2022 and install two more horizontal SVE wells to assist in source area soil contamination reduction. The horizontal SVE wells were installed to lengths of 260 feet (ft) and 300 ft beneath the building, also implementing blind installation technologies. As a result, the installation process eliminated interferences with any on-site activities relating to business operations while still providing maximum screen contact with the source of the soil contamination. Directional Technologies provided their professional support in the operation of the horizontal remediation system to maximize the performance of each SVE well and reduce soil contamination levels. Figure 2 illustrates how Directional Technologies implemented their proprietary screen design software to precisely acquire the target flow rates for each horizontal SVE well.
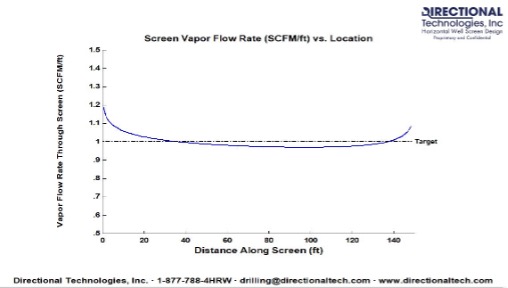
Results:
Directional Technologies was able to perform the installation of the two horizontal SVE wells ahead of schedule despite the physical challenges presented at the site. The final horizontal well design provided successful results in remediating the source area soil contamination after system start-up. Remediation continues at this site via the horizontal SVE wells and continues to reduce source area soil contamination. Through the ability to install the wells blindly beneath the existing facility, the source area soil contamination has been controlled and reduced, ultimately reducing the potential for vapor intrusion into the existing facility.
How can the advantages offered by decades of technological advancement in the field of horizontal wells benefit your project? Call our horizontal remediation well experts at 1-877-788-4479 to discuss your current project needs, or click HERE to complete our online form.
Written by: Elliott Andelman, Environmental Scientist