Horizontal remediation wells (HRWs) are often most associated with accessing seemingly inaccessible areas of a site, such as beneath active buildings, railroads, roadways, and more. Though useful in these situations, the benefits of HRWs go far beyond accessibility. Generally, we discover that the performance scale starts to tip in favor of HRWs when five or more vertical wells are proposed for remediation purposes. At this point, consultants often discover a decrease in overall material costs and an increase in performance compared to vertical solutions. The supplemental case studies in this article explore sites where access was not an issue at all, and yet HRWs were the best choice for efficient and rapid remediation.
Case Study 1: Horizontal Hydraulic Barrier Replaces Vertical System
At a landfill site, a series of vertical extraction wells acting as a hydraulic barrier were failing and needed replacement. Without a proper barrier in place, 1,4-dioxane leachate was migrating off-site with the risk of impacting several residential neighborhoods. Rather than re-installing several vertical wells in a row, providing limited screen contact with the target lithologic zone, the consultants replaced the proposed vertical wells with one horizontal extraction well. The total well length was 800 feet, with 500 feet of continuous horizontal screen placed directly at the target depth. The well successfully intercepted the contaminants, eliminating excess material costs by removing several vertical wells and providing a more comprehensive radius of influence.
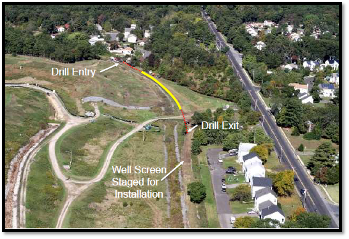
By having one continuous screen in the target zone, the horizontal well helped prevent gaps in the hydraulic barrier caused by ROI communication issues amongst the proposed vertical wells. Utilizing HRWs as part of a barrier design is common in other applications as well. This method has been successfully implemented at other sites for air sparge and soil vapor extraction barriers to prevent migration of the contaminant plume into nearby sensitive receptors, such as homes, businesses, or rivers.
Case Study 2: Horizontal Permeable Reactive Barrier Installation
Work-area space was limited for a horizontal permeable reactive barrier (PRB) installation that took place at a former dry-cleaning chlorinated solvent site. Source area contamination was actively migrating southeast and onto adjacent properties. As part of a pilot study, one horizontal injection well was installed perpendicular to the migration pathway along the widest portion of the plume. The target zone was a transmissive 3’-4’ thick sandy layer, roughly 25 feet below the ground surface, that laid on top of impermeable bedrock.
At this site, the client was sensitive to on-site activities and associated restoration to their parking lot. By installing one HRW, multiple vertical well heads at the surface were reduced to one horizontal well head, conveniently placed in the corner of the parking lot. Once activated, the horizontal well achieved a radius of influence of 20’-25’, fully encapsulating the entire transmissive zone and effectively preventing further migration of the source area contamination.
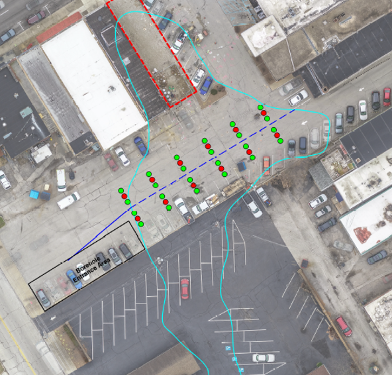
In each of these case studies, a single horizontal well was sufficient to meet the performance goals of the project. Neither of the sites had access restraints that would have prevented vertical installations, and yet horizontal wells proved to be the best option for performance and budget.
How can the advantages offered by decades of technological advancement in the field of horizontal wells benefit your project? Call our horizontal remediation well experts at 1-877-788-4479 to discuss your current project needs or email us at drilling@directionaltech.com with questions, review case studies, and to learn more.
Written by: Elliott Andelman, Professional Geologist