Horizontal wells are often associated with soil vapor extraction, air sparging, and injections due to their ability to provide access beneath buildings; however, due to their increased screen length and geometric compatibility, they present an advanced solution to hydraulic control applications. Whether the goal is groundwater extraction for a pump-and-treat system, or a downgradient hydraulic barrier, one horizontal well can outperform an entire line of vertical wells in recovery.
When a hydraulic barrier is proposed for a site, it is likely that at least 5, 10, or more vertical wells would be required to accomplish the task. Even after installation, a line of vertical wells requires preferential communication to effectively prevent groundwater migration. Any variance of heterogeneity between the wells may cause a break in the barrier, allowing the groundwater and any associated contaminants to freely pass through the gaps. One horizontal well, however, can replace an entire line of vertical extraction wells. Since the screen is continuous along the length of one horizontal well, communication concerns between the screen and the surrounding medium are effectively eliminated. Compared to vertical, costs are reduced as less well materials are required and the thoroughness of the barrier is uncompromised.
Geometric Compatibility
Horizontal wells are significantly more geometrically compatible with target water-bearing zones. Rather than being perpendicular to the groundwater flow, they are parallel. Groundwater migration typically occurs within the specific subsurface zones that are more hydraulically conductive. The geologic formations responsible for increased conductivity are almost always more laterally extensive, with a limited vertical profile. It makes sense, then, to install a well that is geometrically compatible with the water-bearing zone. One horizontal well can achieve a radius of influence (ROI) of several tens of feet on average, so even if the vertical profile is extensive, horizontal wells are more than capable of encompassing the entire vertical extent of the target water bearing zone.
Case Study: HRWs Target Thin Recovery Zone
A client was challenged with the task of enhancing the effectiveness of an existing remedial treatment system. In a decision involving multiple solutions, horizontal wells were selected as the implemented solution due to their greater capacity to recover groundwater in the thin target zone. Volatile organic carbons (VOCs) in the groundwater were escaping the existing, yet failing, vertical extraction system. As a result, there was a growing threat of off-site migration into a nearby river system.
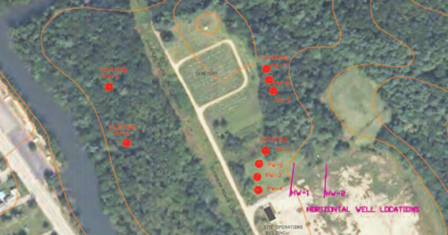
The target geologic layer consisted primarily of fine sand, with some interbedded silt and coarse sand sitting directly above bedrock. Real-time analysis of soil cuttings, separated from drilling fluid returns, was used to confirm and adjust the drill path. Soil analysis, along with precision walk-over locating technology, ensured that the wells were precisely installed within the target zone.
Extensive development of the horizontal well screens by dispersing residual drilling fluids and removing fine materials ensured maximum communication between the well and the surrounding formation. Since the vertical profile of the target zone was thin, horizontal wells were the appropriate geometrical solution to a difficult problem. The alternative would have been tens of vertical wells, each with only a few feet of screen. Once operational, the performance of the horizontal wells more than supplemented the failing vertical system already in place. As a result, the contaminated water was prevented from migrating past the barrier so that a focus on the source-area remediation could resume.
How can the advantages offered by decades of technological advancement in the field of horizontal wells benefit your project? Call our horizontal remediation well experts at 1-877-788-4479 to discuss your current project needs or email us at drilling@directionaltech.com with questions.
Written by: Elliott Andelman, Professional Geologist