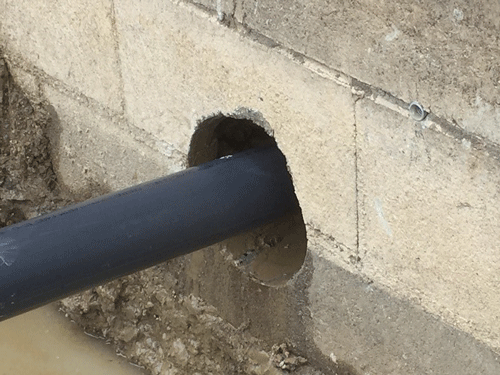
Our client, Chris Bade with ASI Environmental in Ludington, Michigan, selected horizontal remediation wells to prevent loss of revenue to a busy manufacturing facility. Horizontal sub-slab vapor extraction wells for a TCE vapor recovery system were installed from outside of the facility with horizontal directional drilling methods, allowing manufacturing operations to continue unimpeded.
Installation of horizontal remediation wells with directional drilling prevented an estimated 200 hours of manufacturing downtime.
Introduction
Success in the manufacturing industry is reliant on production. Facility shutdown and equipment downtime are the most significant risks to profitable operations. Therefore, downtime for environmental work at many facilities is not an option. This case study demonstrates how horizontal remediation wells installed from outside of the facility alleviated the concern of facility downtime for the remediation system installation.
Background/Challenge
A manufacturing facility in the Midwest was in operation for over 70 years machining a wide variety of stainless-steel products. Prior to environmental regulations, the facility used in-ground degreaser pits as part of their operations which resulted in significant TCE impacted soil and groundwater. Based on subsequent environmental investigations, vapor intrusion posed indoor air quality issues for workers. The facility is crowded with machining equipment and operated two shifts around the clock, complicating the option for a vapor mitigation system to be installed through the facility foundation slabs.
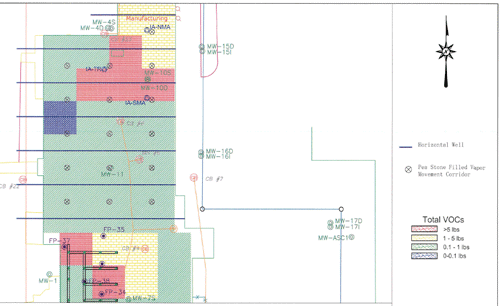
Solution
ASI Environmental contacted Directional Technologies to install seven (7) horizontal sub-slab vapor extraction wells. The horizontal SVE wells were constructed of 3-inch diameter schedule 80 PVC. Beginning from outside of the building, the horizontal SVE wells were installed at depths of 5 feet to 9 feet below ground surface (bgs). The horizontal SVE wells were installed via blind (single-ended) method, meaning exit points on the other side of the building were not required. Directional Technologies used proprietary software to design custom machine slotted horizontal well screen for even flow rates across the screened interval. ASI provided access to the sub-slab soils by coring 8-inch holes through the concrete footing walls, from where the horizontal bores could then be advanced.
Minimal interior access required
The only interior access needed was for the Directional Technologies locator to enter portions of the building to track the advancement of the horizontal direction drill bit beneath the concrete floor slab. The drill bit was tracked with a walk-over locating system and steered toward the target areas for installation of horizontal well screen. The horizontal well installation portion of the project was completed within six days.
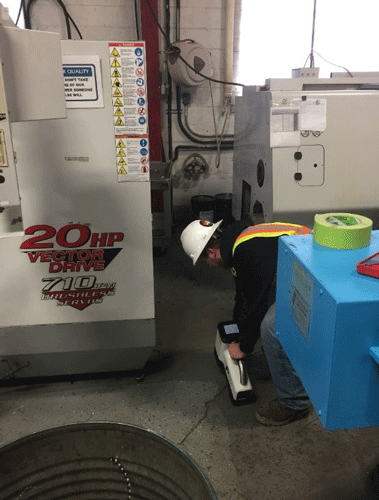